BLS 4000next half mask
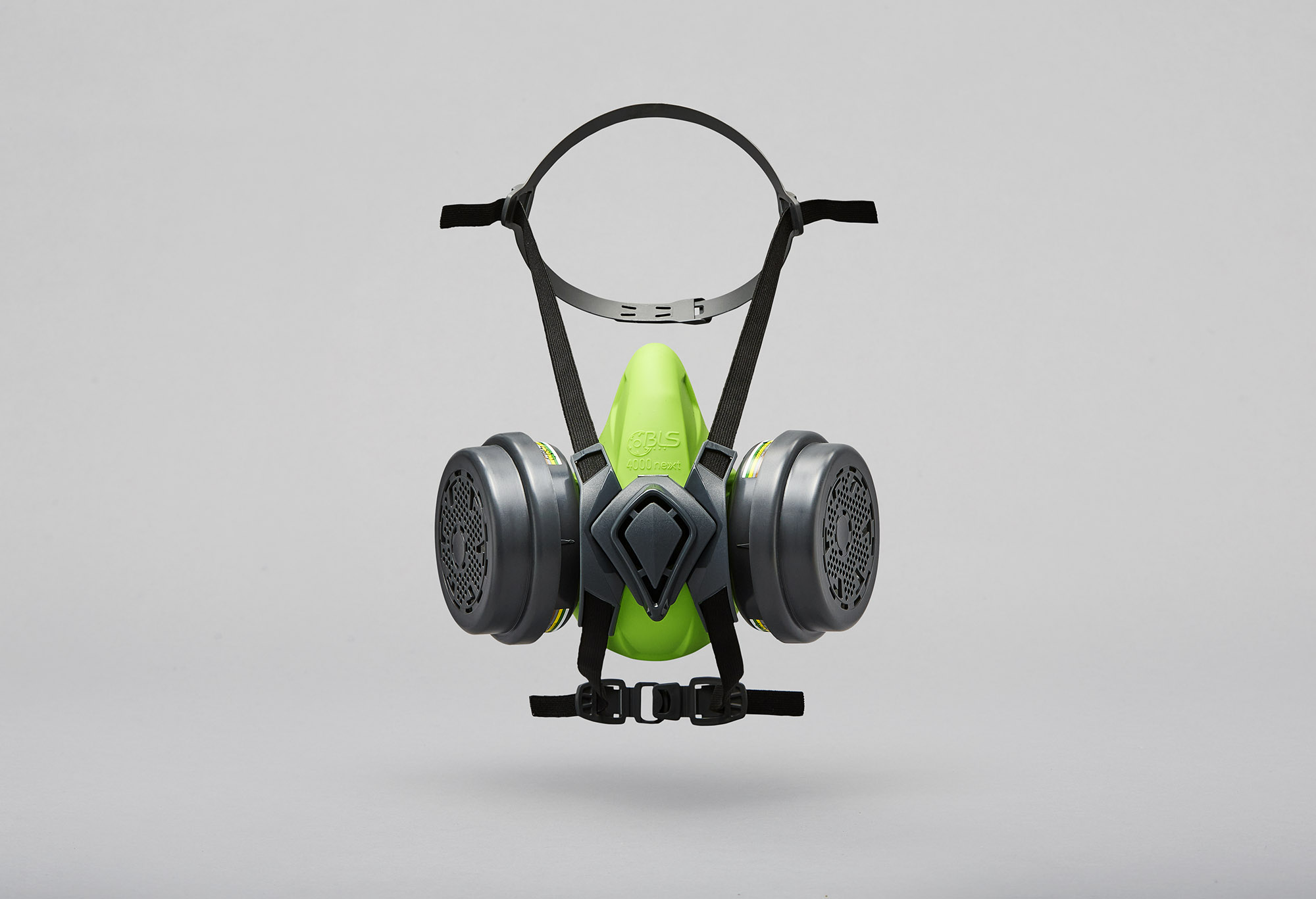
Certifications
CE 0426
EN 140:2000
Product design and manufacture of a Semi-mask for industrial use with replaceable filters for protection against dust, fumes and gases.
0. NDF Impact
1. PRODUCT DEVELOPMENT BRIEF
The BLS Group customer needed a redesign of one of their existing half-masks. The goals were to reduce the production cost of each product while improving its performance and aesthetics. The project would be presented at a 2018 trade show in Paris.
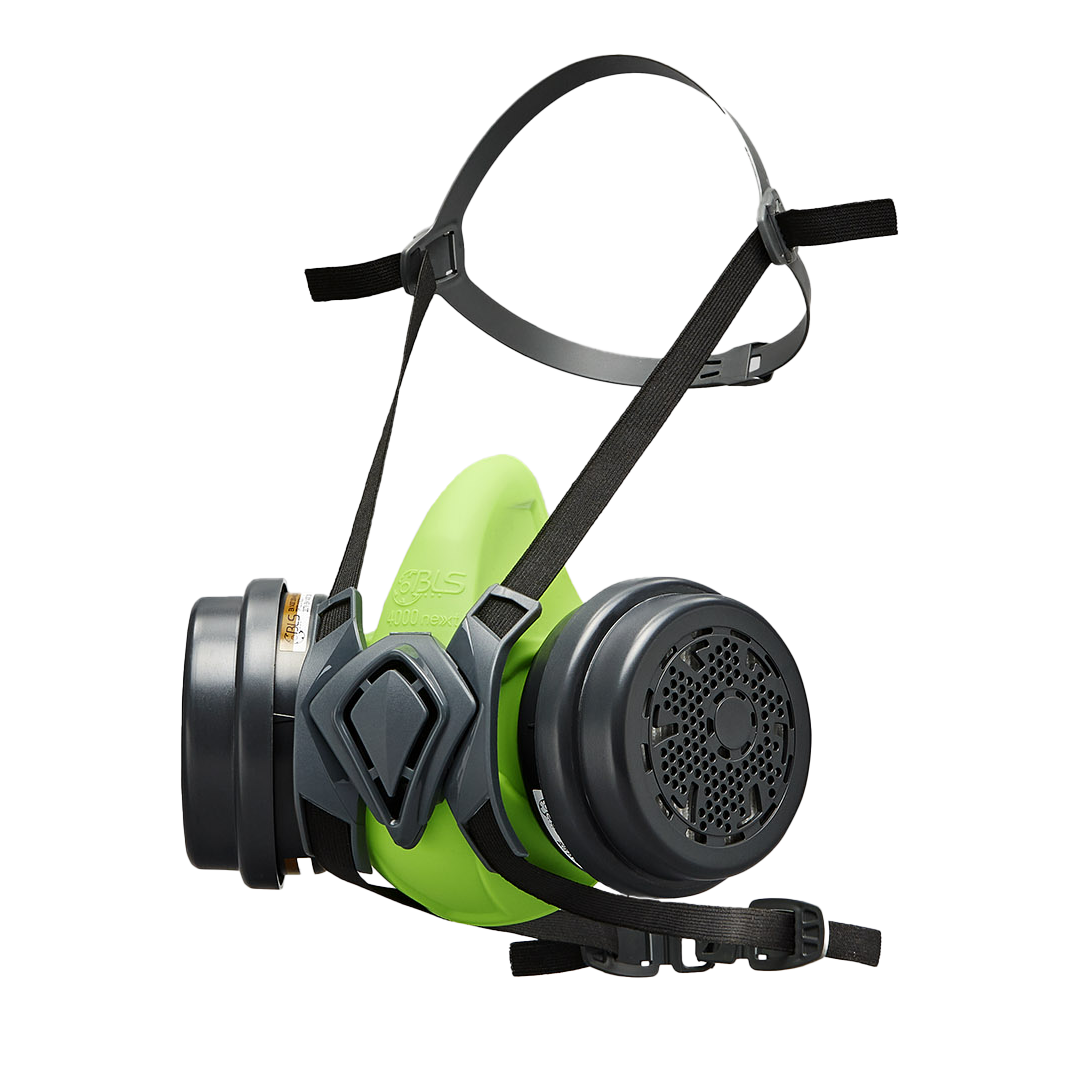
2. DESIGN CHALLENGES
As already highlighted in the client’s brief, the design challenges are located on various levels of the design.
Weight optimization
Finding the balance between material, thickness, and component weight without losing structural properties of the mask (e.g., oronasal)
Process improvement
Increasing product performance should in no way affect that of the production process
Economic constraints
New product implementation investments were subject to precise economic and time budgets
3. DESIGN PROCESS
Scanning the project into its most relevant design phases.
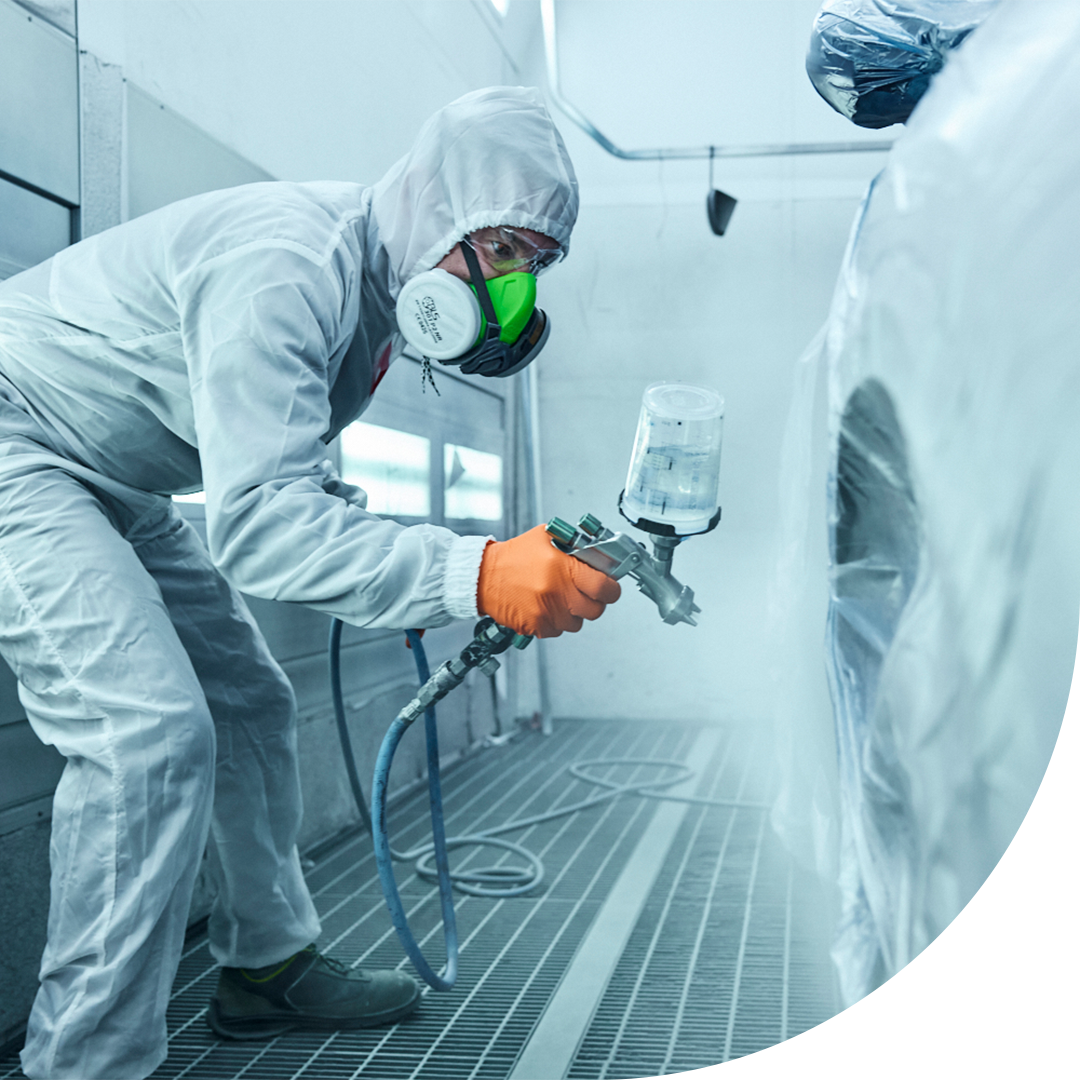
Product Development Research
The process began with a cross-user analysis together with the client. User journeys, related needs and design insights were defined. This analysis, together with a competitive study and analysis of market feedback from past years, led to an optimization of the client’s brief.
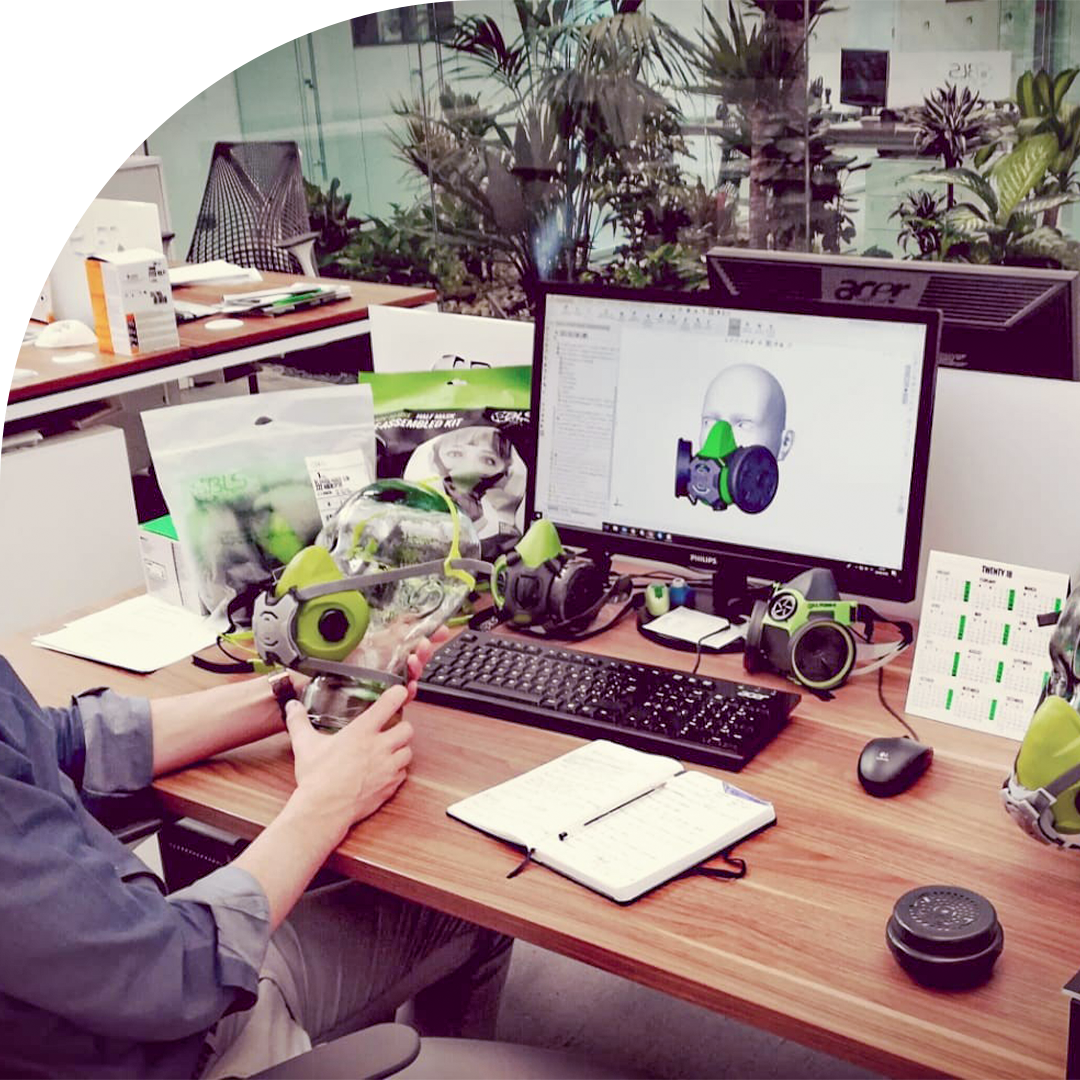
Concept development
The concept study involved every single component, so as to bring improvements to every aspect of the product.
After an initial design phase, an internal realization of a POC to be shown to the client was achieved.
Then the first tests were carried out through the prototype and iterative cycles of improvements and revision.
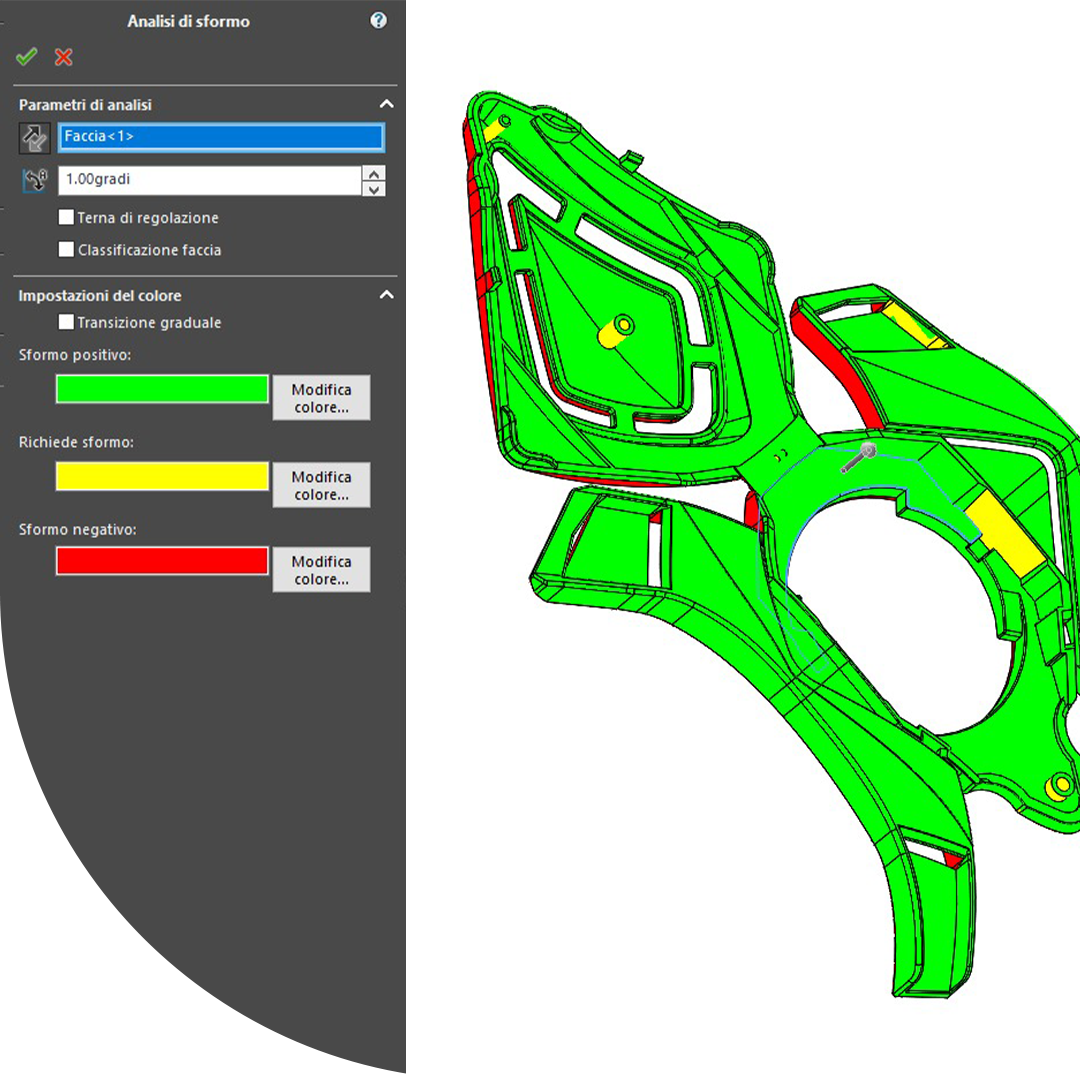
Product Engineering
The product development involved the engineering of the individual components. The technical details for injection molding, such as draft angles and position of the ejectors, and the aesthetic details for photoetching of the molds were defined, dialoguing with the various suppliers The project was concluded with the delivery to the customer of all the technical documentation necessary to put the product into production.
4. PROJECT OUTPUTS
From the decomposition of the initial problems, some design solutions were proposed that were able to convert technical limitations into a structural renewal of the starting product
New shape, same appearance
The aesthetic search for a family feeling with the products in the BLS portfolio led to a result that was new but perfectly aligned with the company style.
The product was also enriched through work on its image that extended to new naming and branding.
Combine to reduce
Two components critical to the product’s creation were assembled and combined into a single component.
This choice resulted in a reduction of the investment on the mold, a drastic cut in the cost of the product, and a logistical optimization of its management.
Environmental impact
Our orientation toward sustainable design allowed us to achieve a result that improved expectations.
Thanks to our philosophy, the product has become disassemblable into all its components, which can be 100% recyclable.
Simpler, faster
A structural simplification of the product made it possible to reduce assembly time and reduce production costs significantly.
Gallery
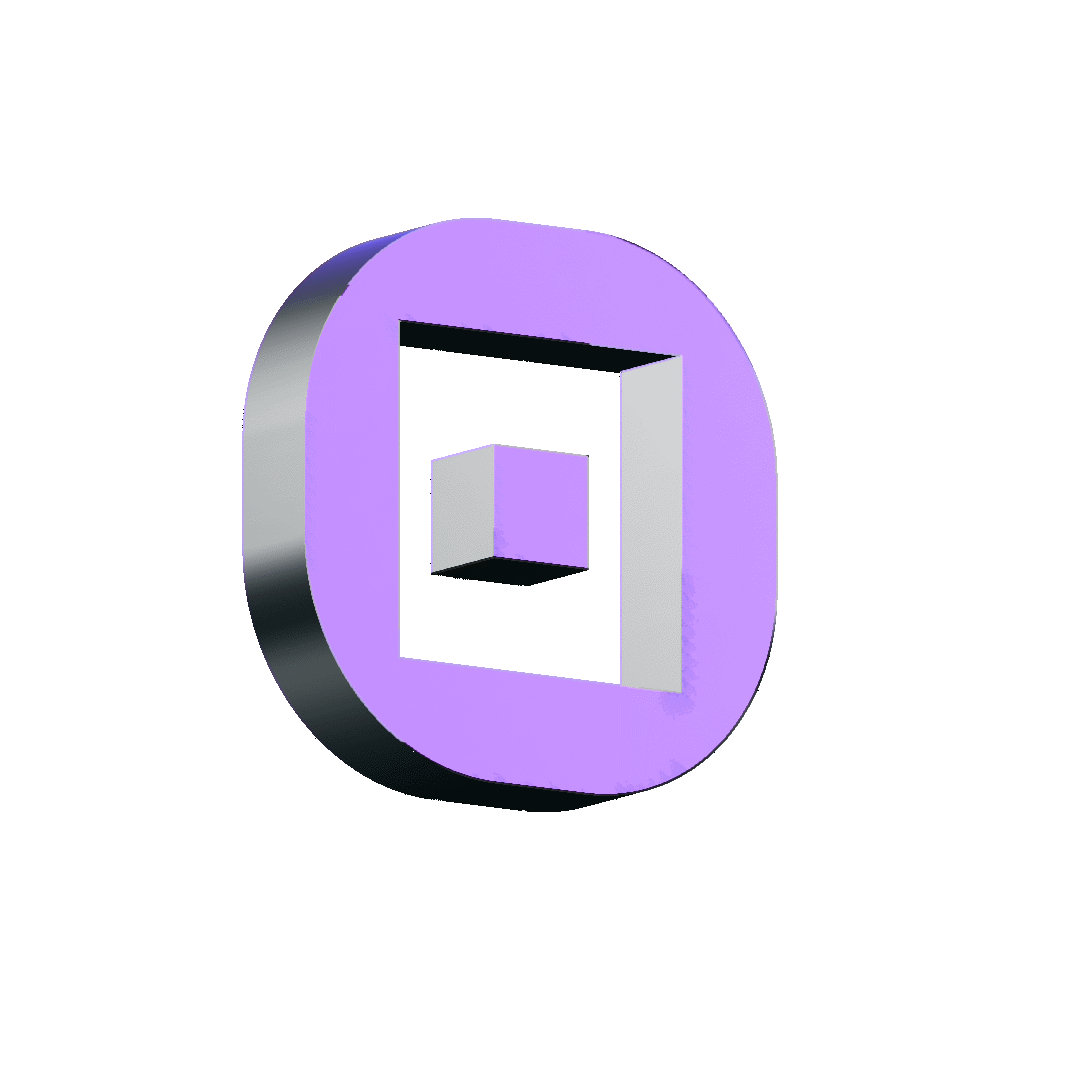
Whatever your project challenge, we respond with innovation and concrete solutions to support and guide you in your advancement and growth process, in line with your objectives.