BLS 2000 Series Full Face Mask
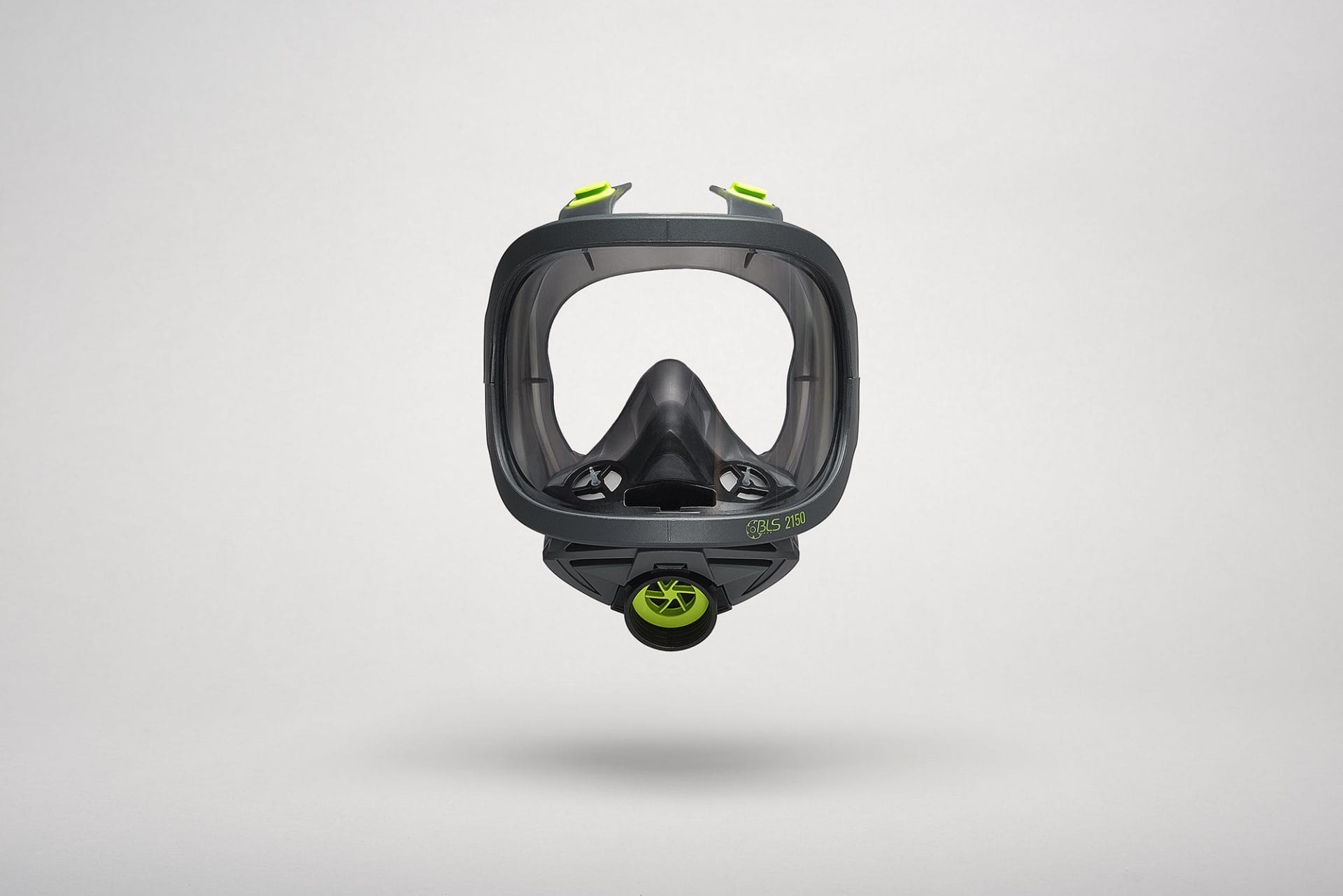
Certifications
CE 0426
UNI EN 136:2000
Product design and manufacture of a full face mask for industrial use with replaceable filters for protection against dust, fumes and gases.
0. NDF Impact
1. PRODUCT DEVELOPMENT BRIEF
The BLS Group customer was intent on redesigning a range of products in the BLS 2000 series in order to be able to break away from the manufacturer of some parts of the product, thus being able to lower the manufacturing costs and reduce the weight of each unit.
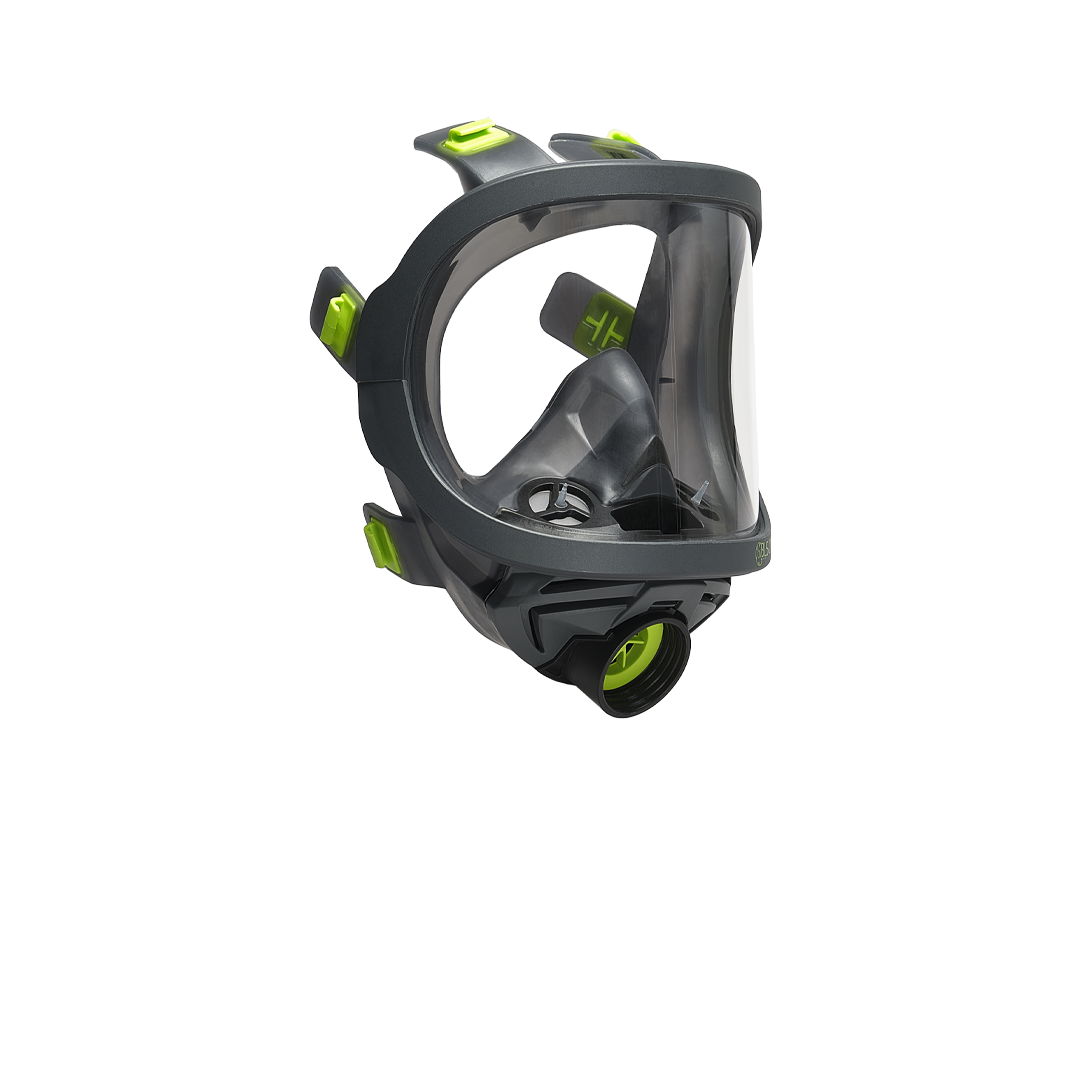
2. DESIGN CHALLENGES
As already pointed out in the client’s brief, the project challenges are located on various levels of the design.
Aesthetic improvement
Carrying out a visible restyling of the product
in order to relaunch it in the market.
Productive Complexity
Operate in the complexity of a multi-part overmolding process while respecting the technical feasibility of the product.
Economic balances
Finding balance between the investment to produce new parts and the reuse of existing components.
3. DESIGN PROCESS
Scanning the project into its most relevant design phases.
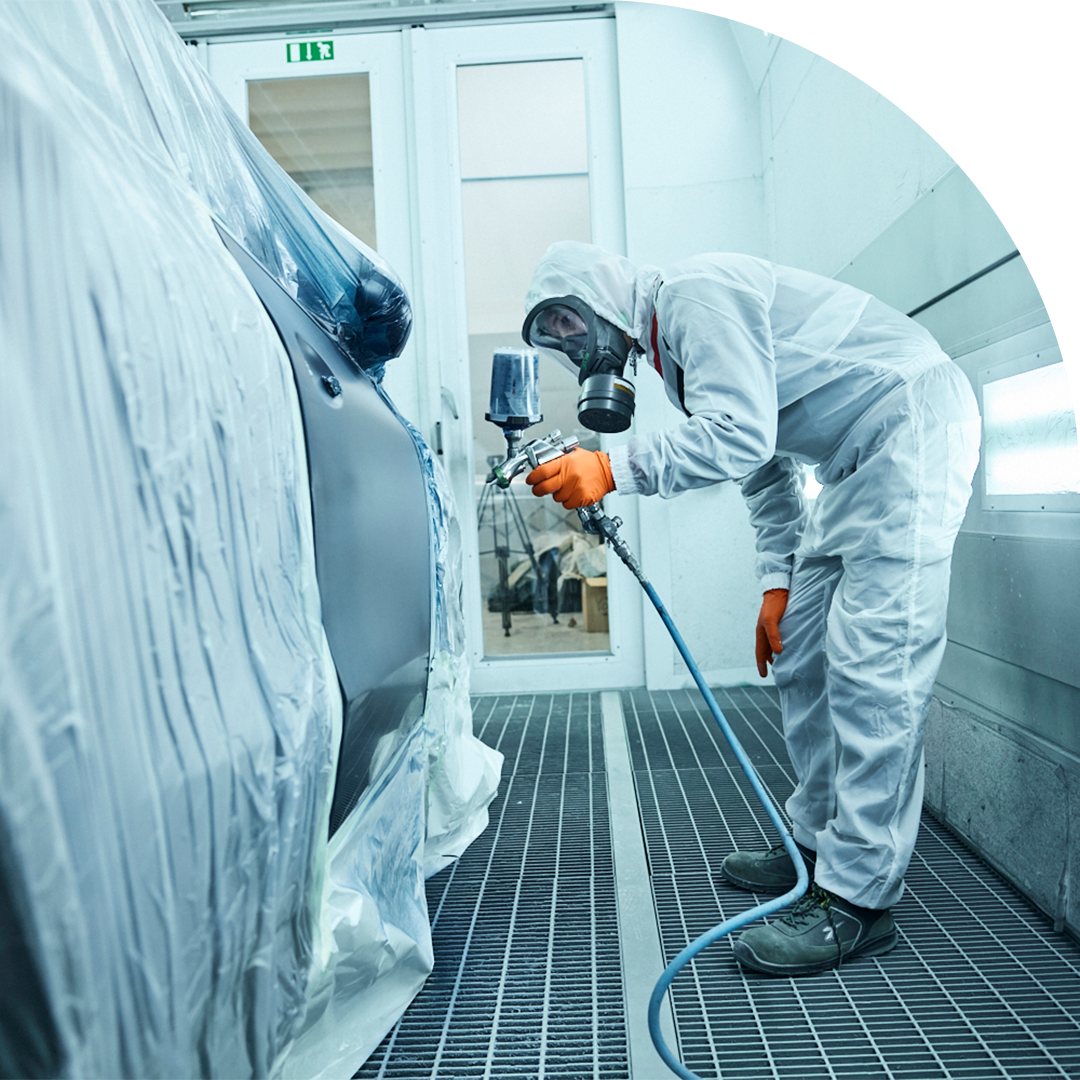
Product Development Research
The process began with a cross-sectional user analysis together with the client. User journeys, related needs and design insights were defined. This analysis, together with a competitive study and analysis of market feedback from past years, led to an optimization of the client’s brief.
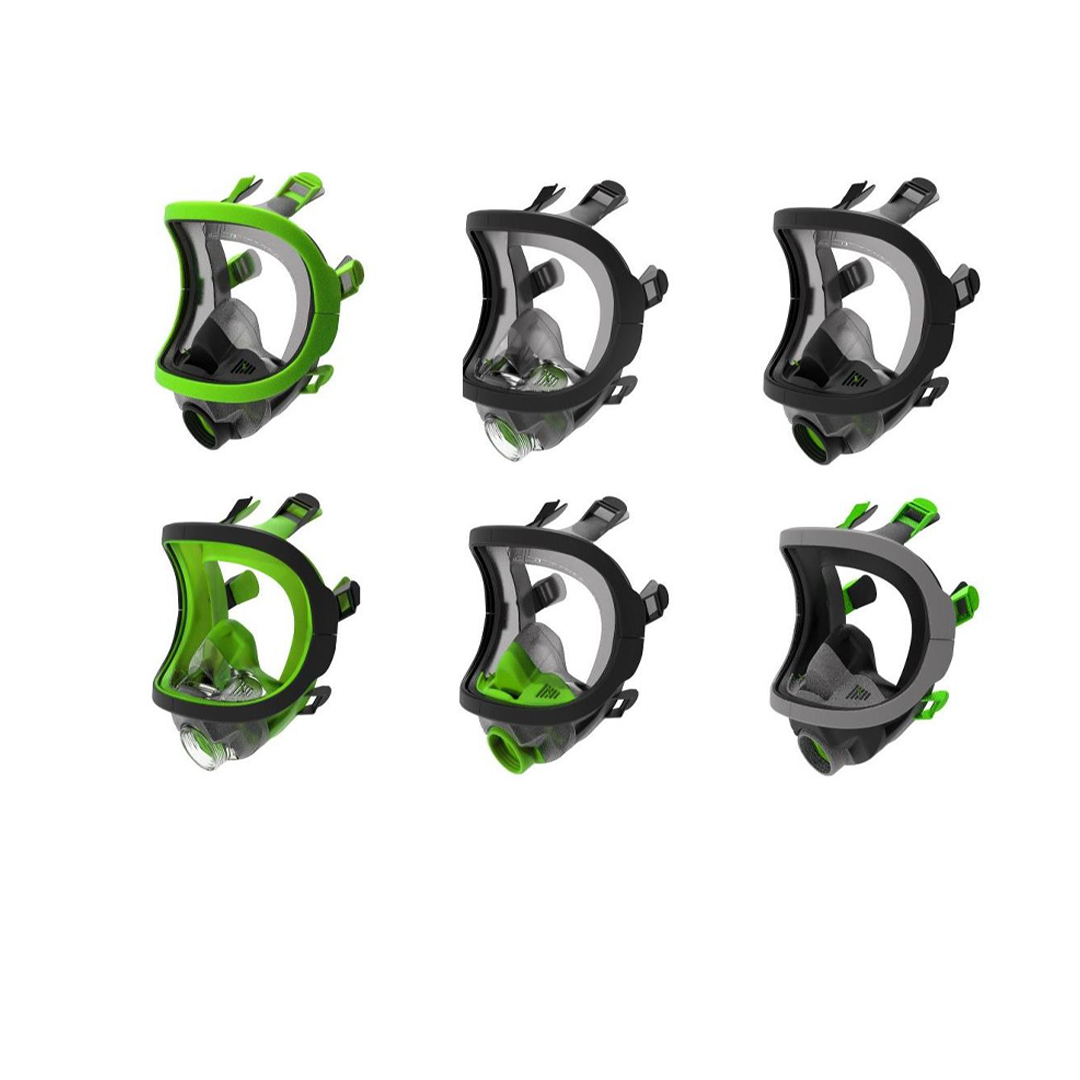
Concept Development
The concept involved a major redesign of many components, but at the same time, in order to optimize investment, some components of the previous model were reused.
After an initial design phase, an internal realization of a POC was made to show to the client.
Then the first tests were carried out through the prototype and iterative cycles of improvements and revision.
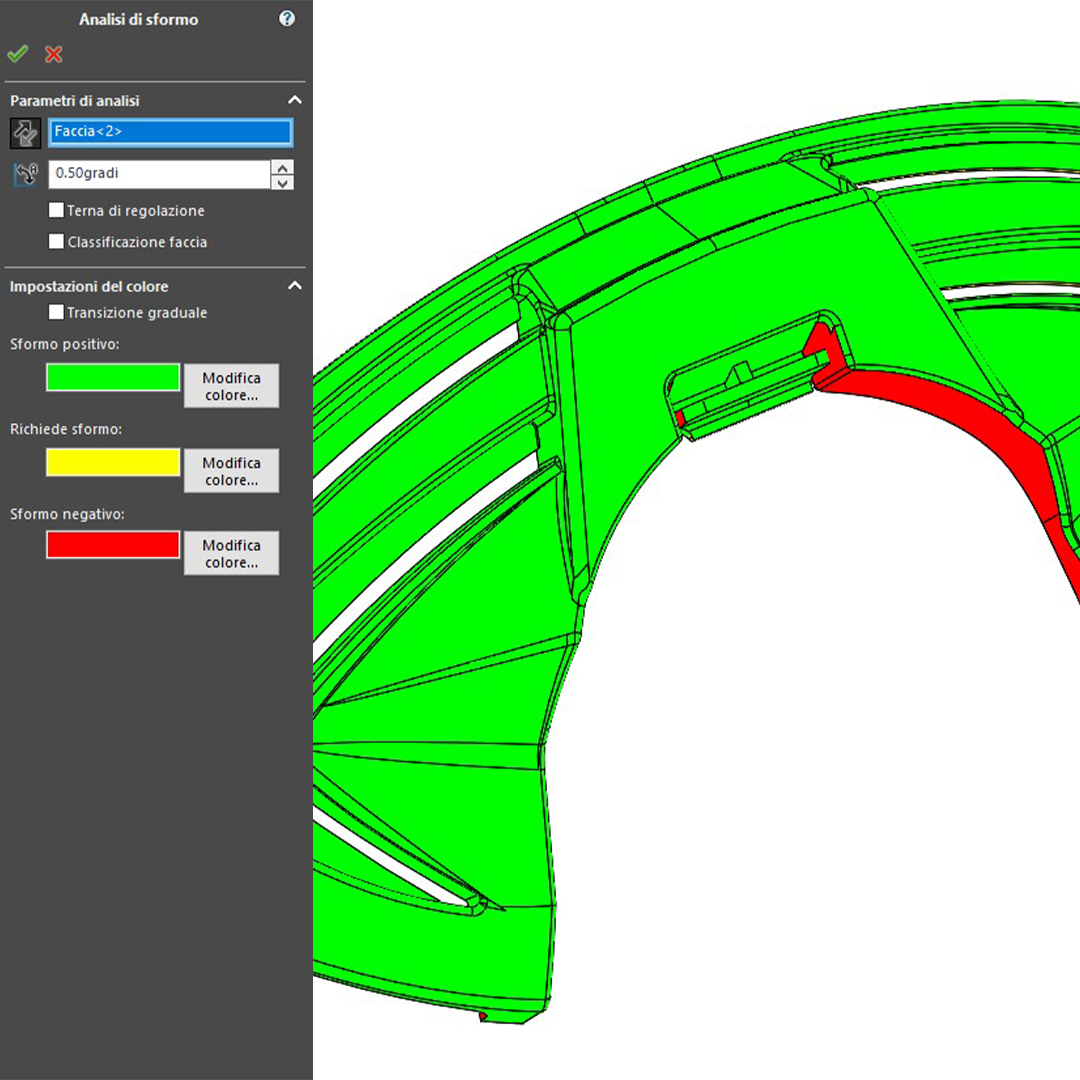
Industrial Product Engineering
The final phase involved the engineering of the individual components. Technical details for injection molding, such as draft angles and position of the ejectors, and aesthetic details for photoetching of the molds were defined in dialogue with various suppliers.
The project was concluded with the delivery to the customer of all the technical documentation required to put the product into production.
4. PROJECT OUTPUTS
From the decomposition of the initial problems, some design solutions were proposed that were able to convert technical limitations into a structural renewal of the starting product.
New valve
For the strategic purposes of the project, we agreed to redesign the most important component of the product, which is its valve.
Through fruitful collaboration with the BLS laboratory, it was possible to design by performing respiratory resistance and leak tests after each intervention.
Improvement of the production process
Through the initial study of the production method, the redesign made changes to the process itself bringing about a consequent optimization.
Adaptation of the product to reuse of components produced for other masks has boosted the economy of scale of the series.
Unique overmolding
The product redesign now allows for a single overmolding of components, leading to a tangible improvement.
Assembly time has consequently been significantly reduced and productivity increased.
Gallery
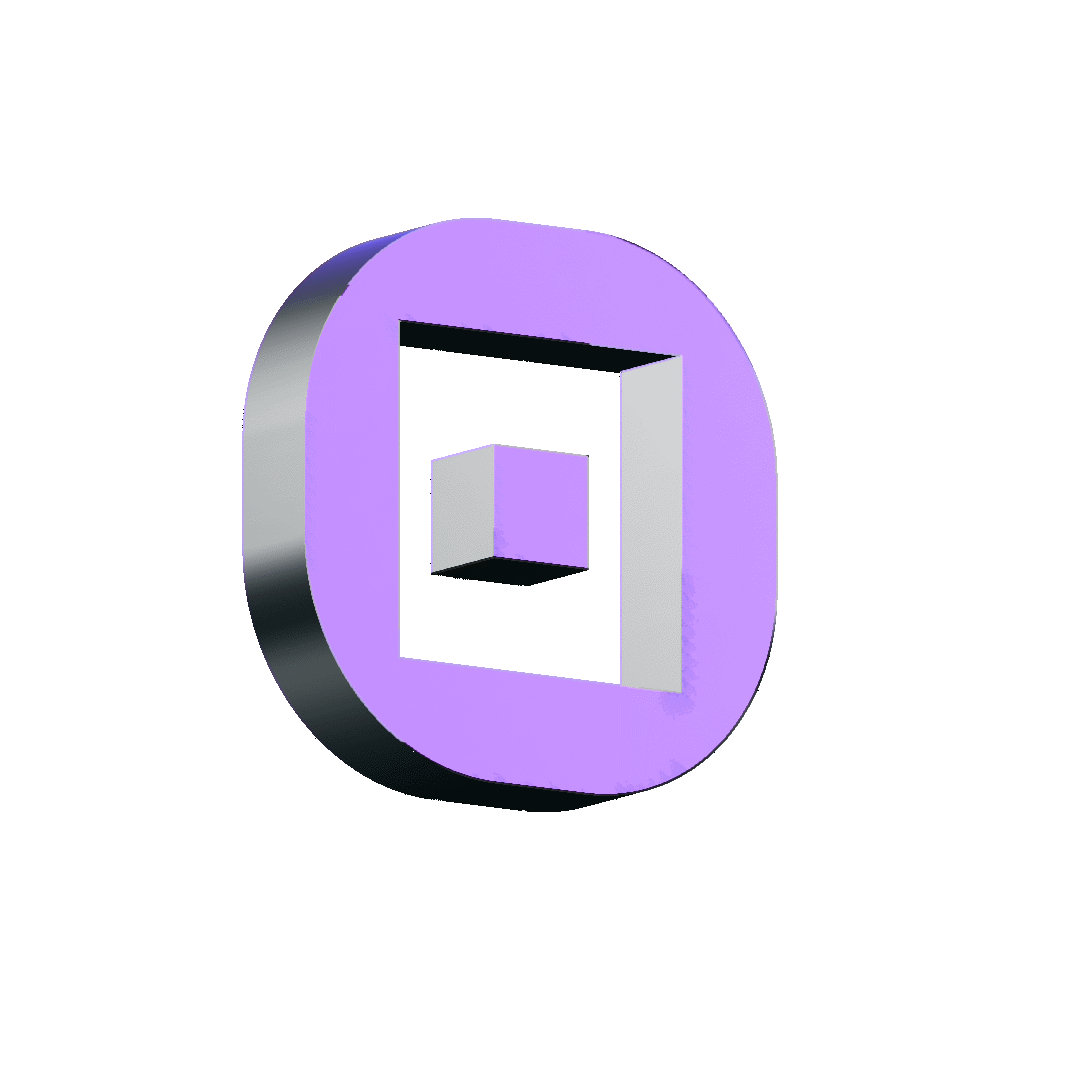
Whatever your project challenge, we respond with innovation and concrete solutions to support and guide you in your advancement and growth process, in line with your objectives.